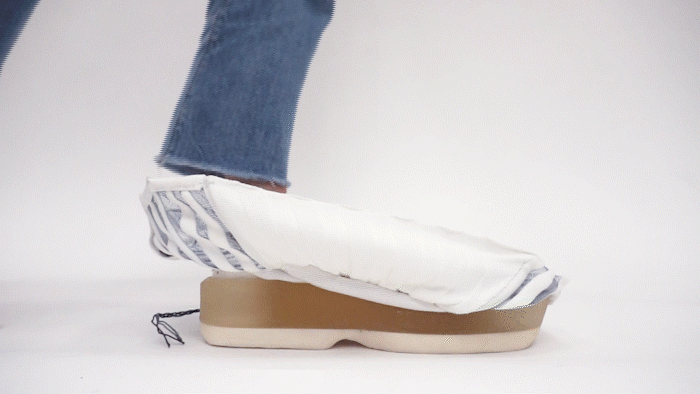
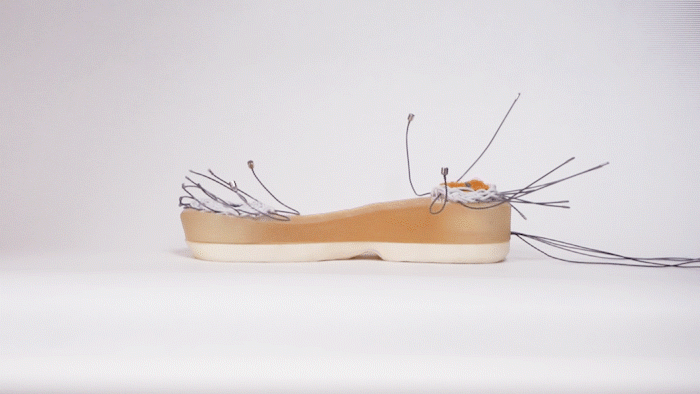
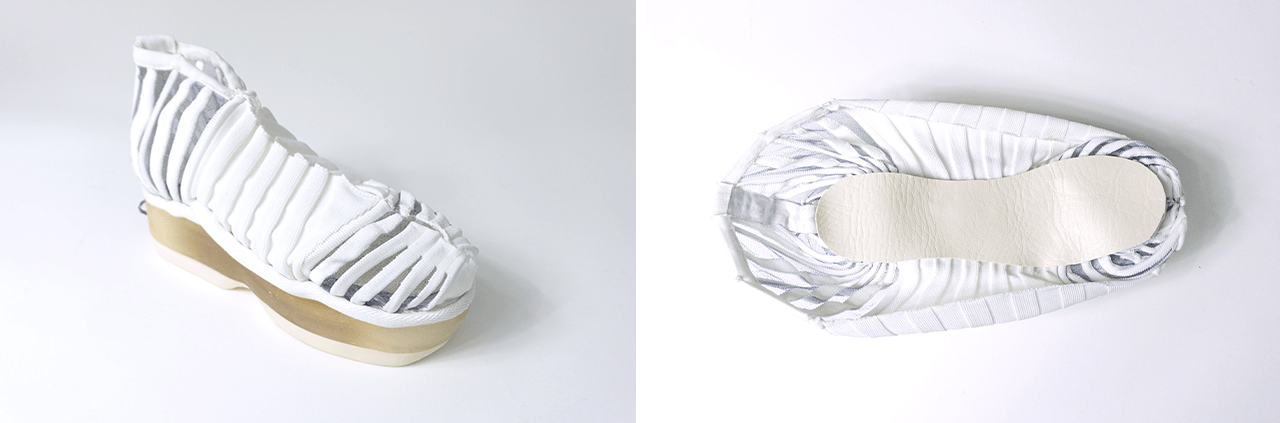
Craft & Material Driven innovation
This project was a quest to find innovation through traditional crafts. Given my obsession with textiles, I honed in on the question: What if textiles can shape-shift based on different contexts? The potential of textile actuators, or “textuators”, can have huge implications for a wide range of soft and semi-soft products, including apparel, sports gears, medical wearables, and architecture.
In the past decade, smart textiles have become a popular medium for scientists, designers, and engineers. The goal of this project was to create shape-shifting textiles and demonstrate their potential through new applications.
Through a series of experiments, a library of passive bistable and compliant actuators was developed using spring wire, elastic yarns, and traditional weaving techniques. These semi-soft mechanisms can be integrated into elastic textiles.
Using these mechanical textiles, I created Bas, or bistable automatic shoe, that snaps onto the foot when the user steps onto the sole and releases open when a trigger is pulled. This concept demonstrates a future where apparel can snap on and off the body, just one of the many potential applications for moving textiles.
Process
The two-thronged approach involved both material research and application development at the same time.
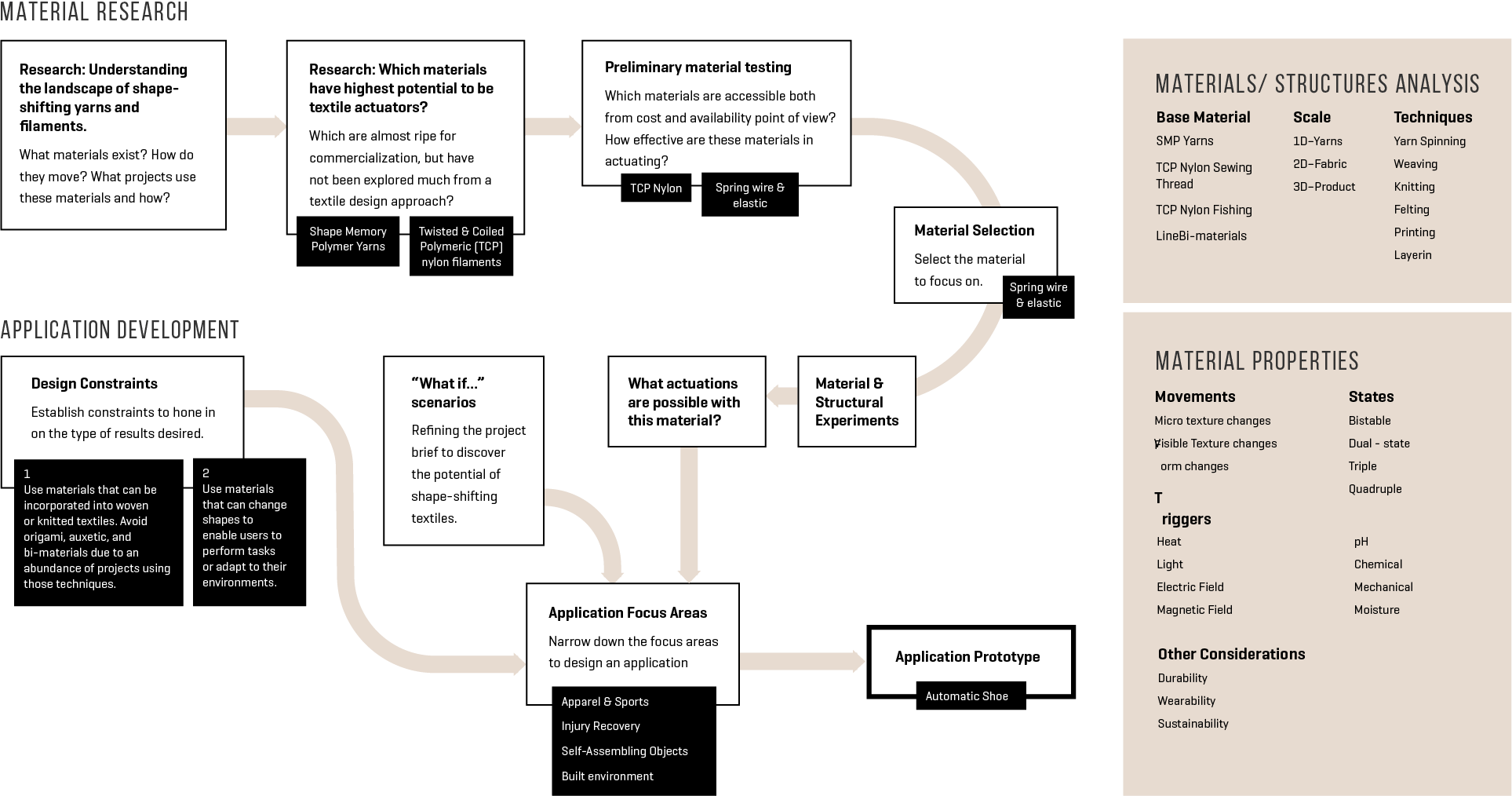
Material Exploration
A library of compliant and/or bistable actuators was developed through extensive experiments. These wireframes can be integrated into knit textiles to create semi-soft actuators. The optimal ones were used to create the automatic shoe.
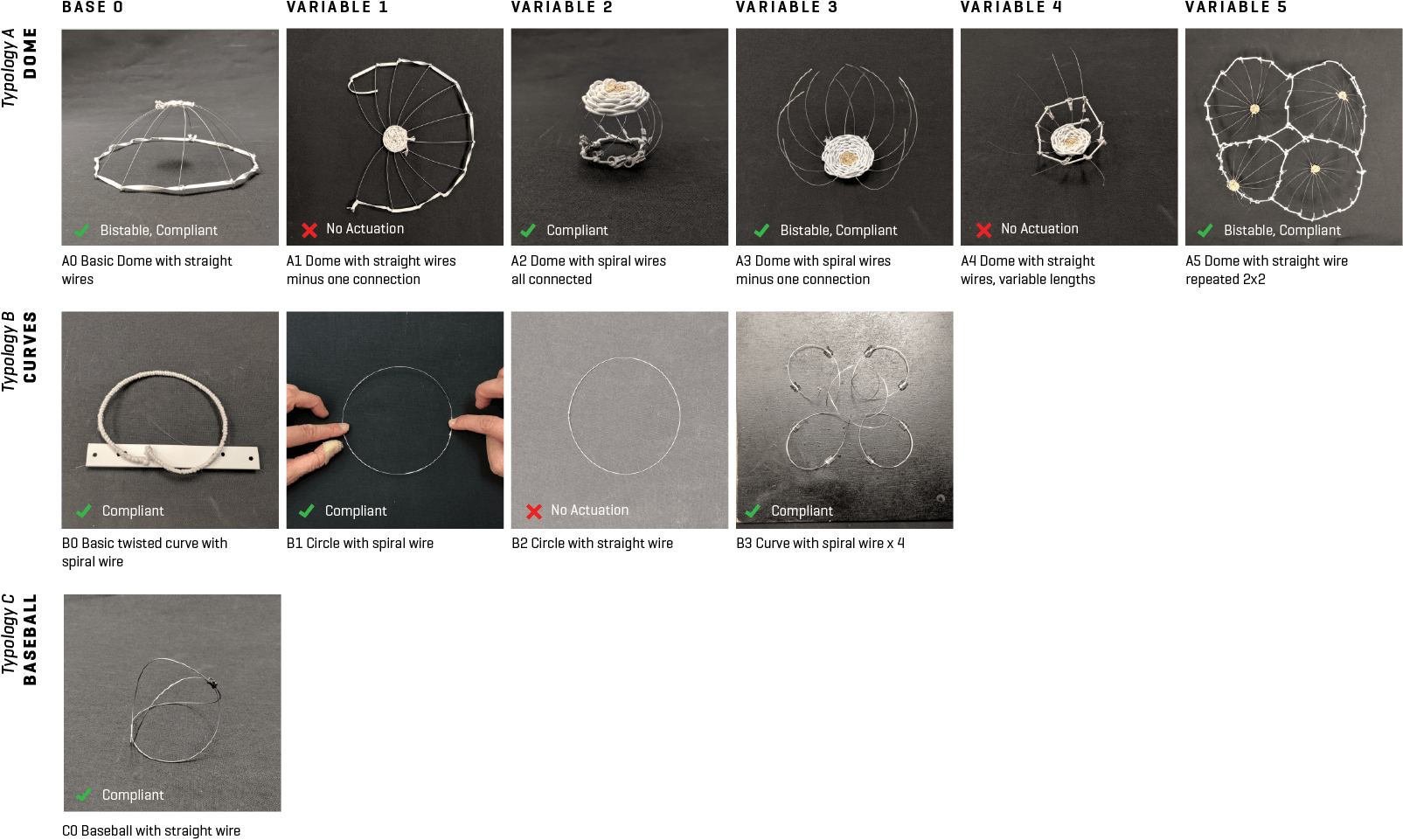
Making of Bas
Shoe Design & Pattern
The original design of the shoe was driven by the skeleton and movement of the textiles, taking an asymmetrical organic shape. This design was later simplified during the textiles knitting phase due to time and budget constraints.
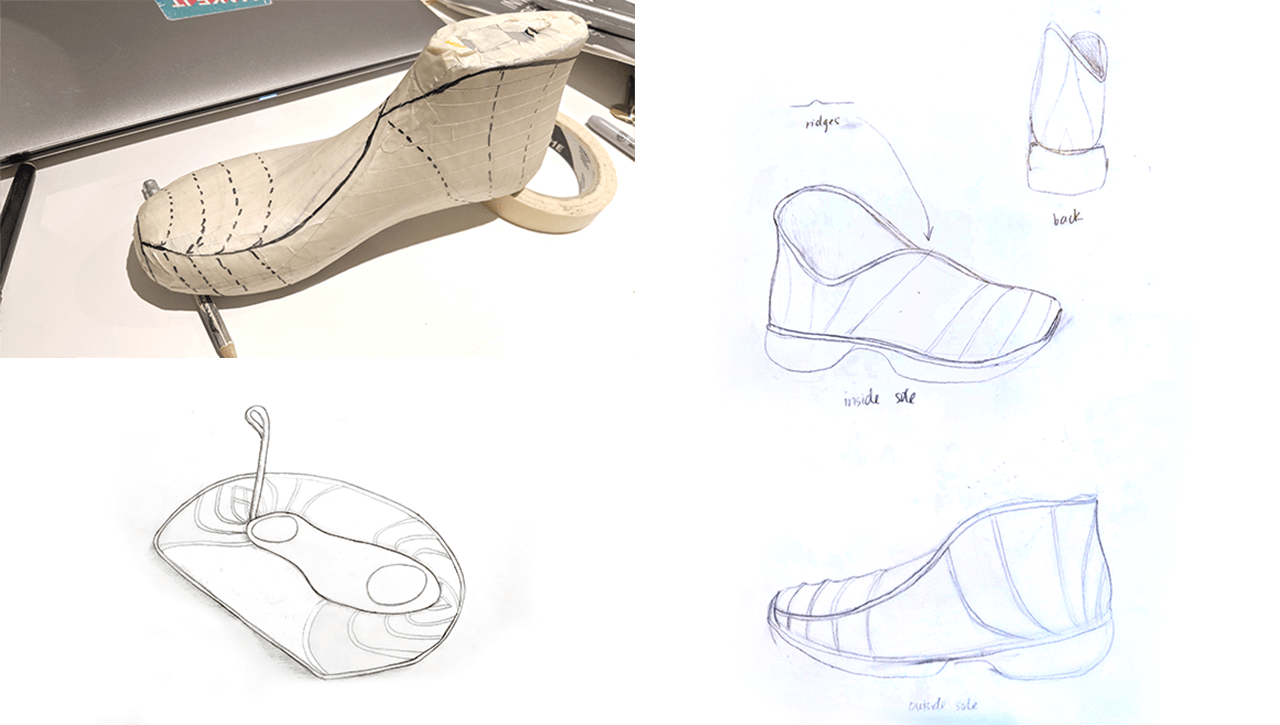
Skeleton
The skeleton took dozens of experiments and iterations to perfect. Using spring wire and elastic cord, the final structure required just a small push to actuate, and had the optimal line of motion for an automatic shoe and the contours of the shoe last.
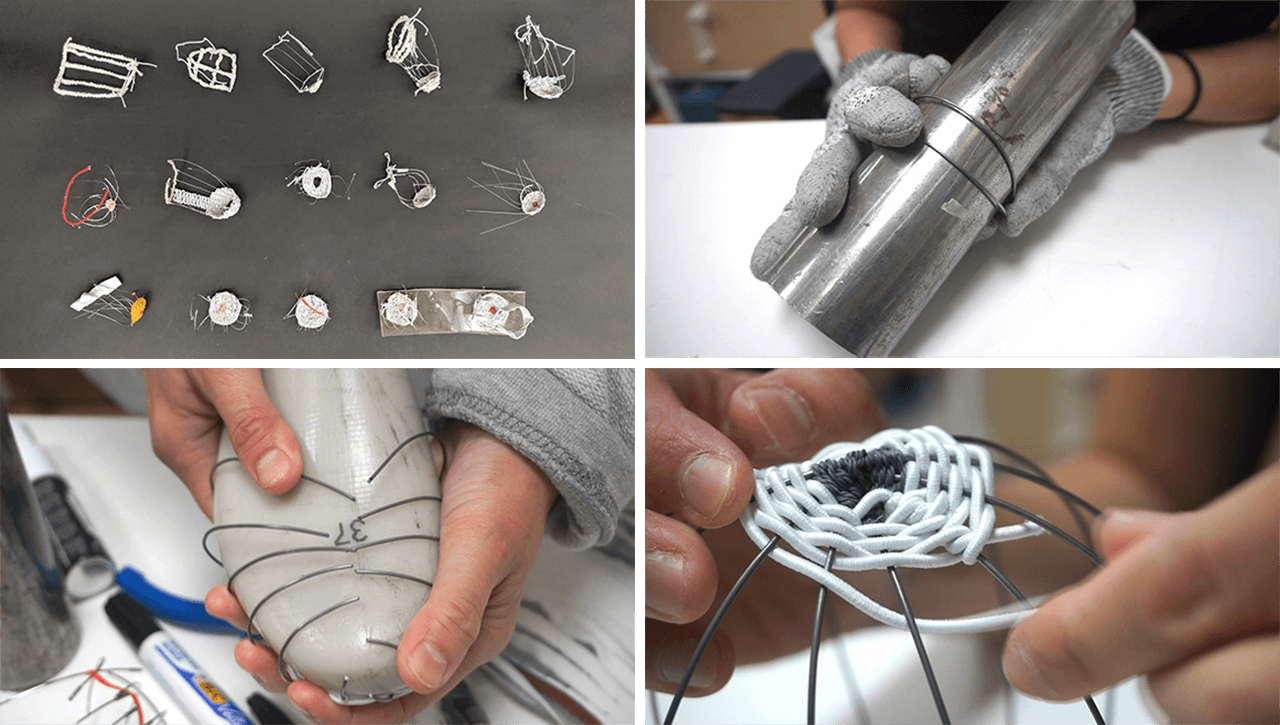
Sole & Release Trigger
The sole encases the release mechanism. First, the mechanisms were modeled in SolidWorks, then 3D printed. The hinges were machined in aluminum. To create the silicon mould, a model was first made in wood. Rubber was cast in the mould to make the final sole.
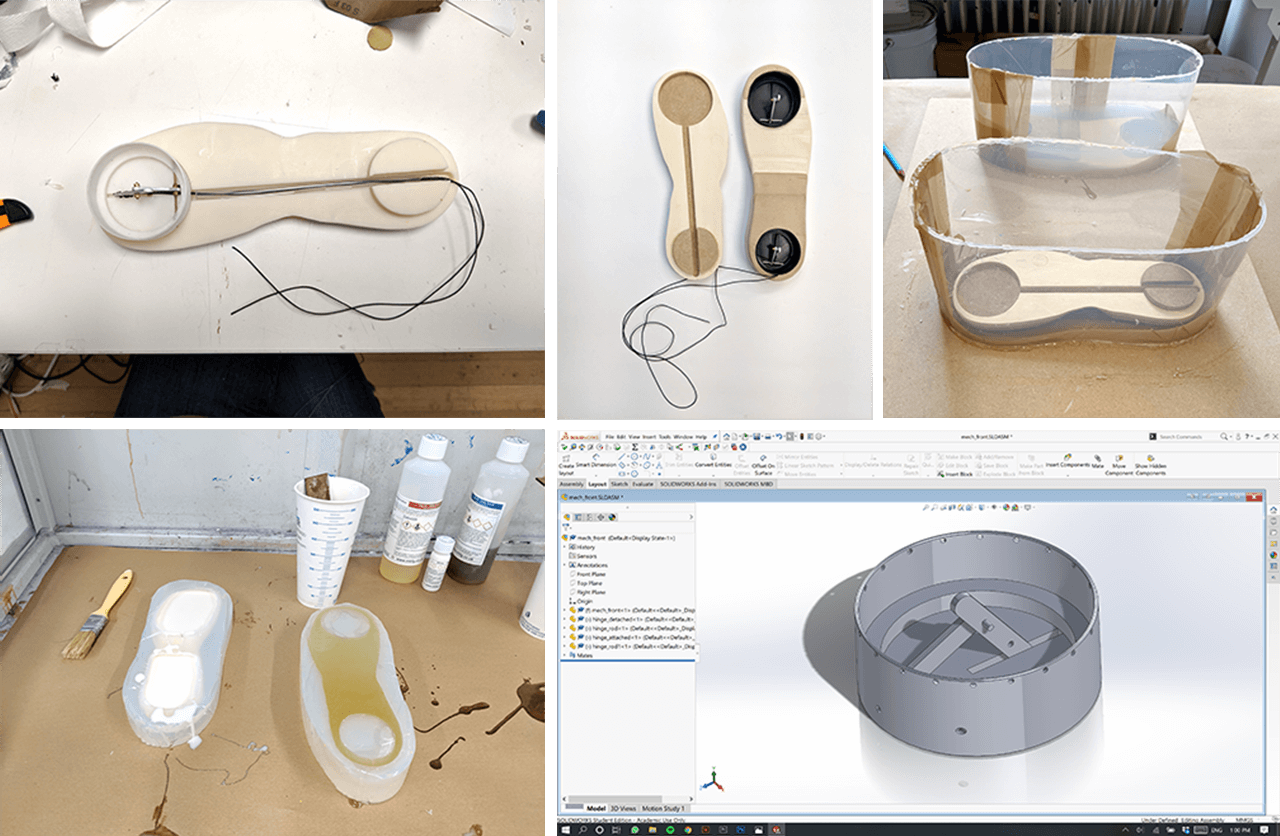
Shoe Upper
Working with Loop Studio in London, a shoe upper was knitted using a Stoll machine that fits the wireframes. The pattern accomodates for expandable ribbing, tunnels for the wires, and an design asethetic that accentuates the textile’s movements.
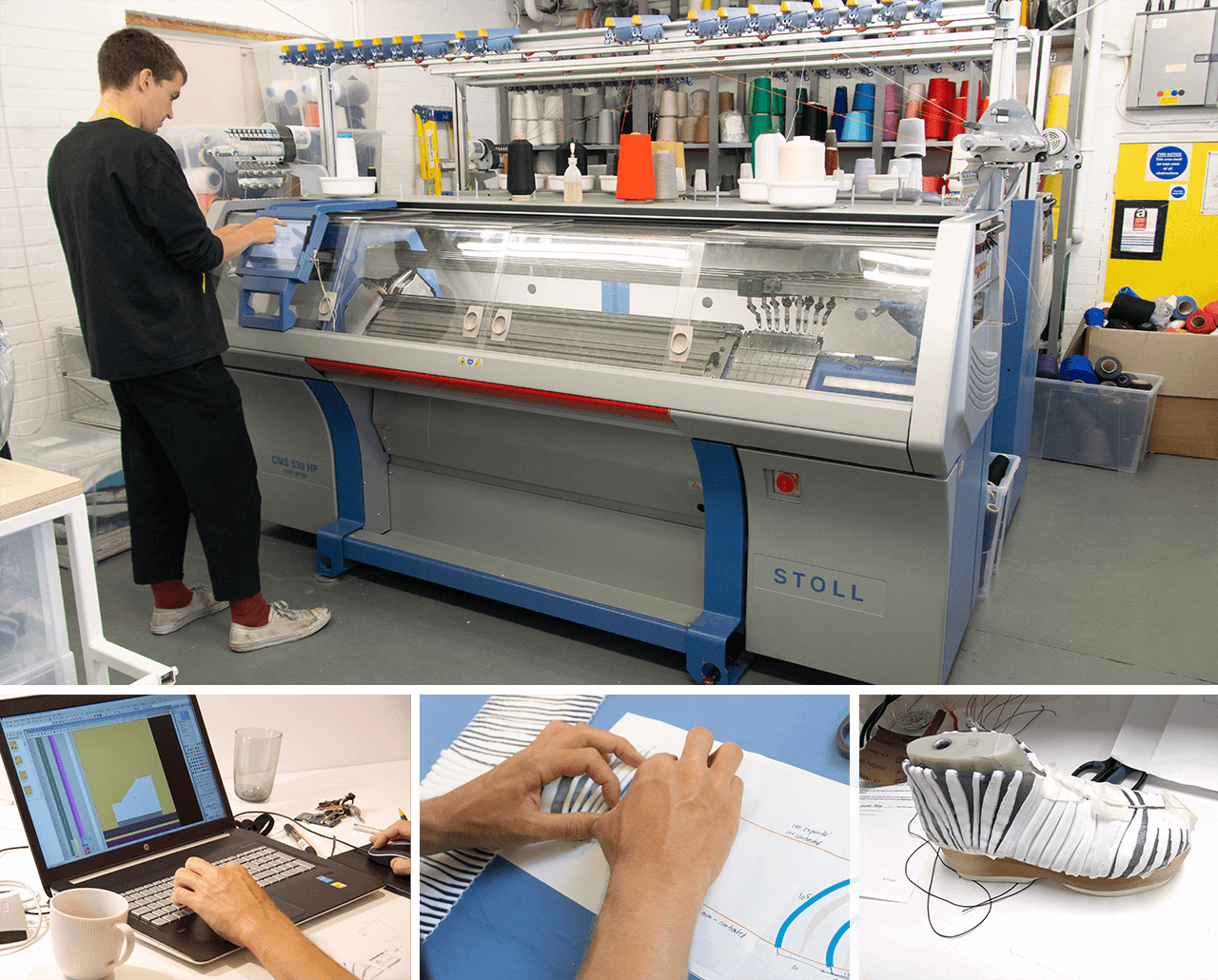
Assembly
After all the parts were finished, it took a couple iterations to assembled the first functional automatic shoe.
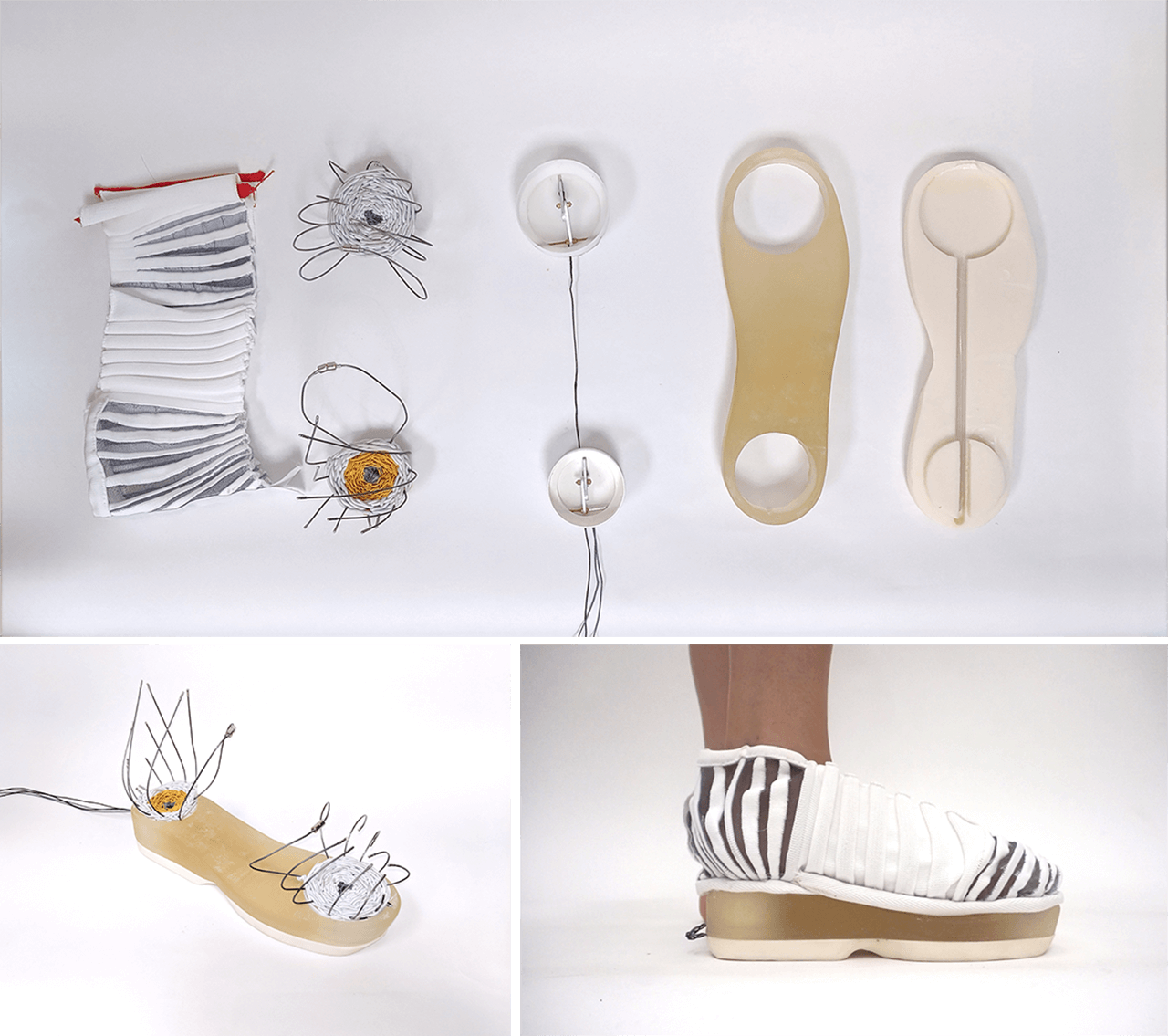